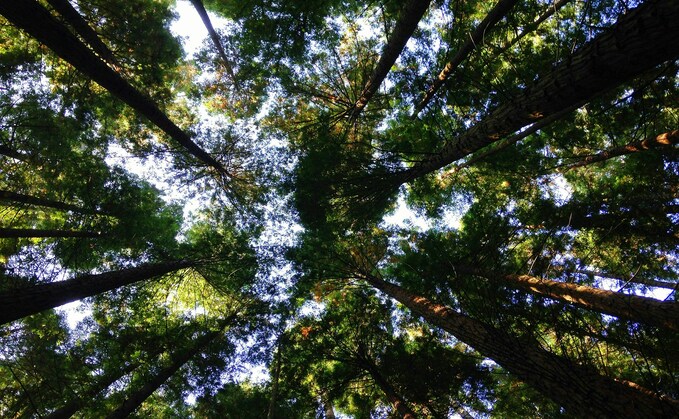
Partner Content: Dow's Victor Zapata discusses what Dow are doing in their commitment to creating circular business models and how they are continuing to look for innovative ways to accelerate a circular economy.
Thinking about plastic pollution and production: INC-4 in Ottawa
This week, the penultimate meeting on the UN's global plastic treaty concluded in Ottawa, Canada. The fourth session of the Intergovernmental Negotiating Committee (INC-4) saw extensive discussions on the issue of plastic pollution.
As the North American Commercial Vice President for Packaging and Specialty Plastics at Dow, I am keen that any progress made at INC-4 in Ottawa recognizes how complex and urgent the plastic waste problem is globally. Collective action by all stakeholders - including governments, the entire value chain, scientific institutions and academia, communities, and financial institutions - will be vital to progress.
At Dow, we recognize just how crucial circularity is to reduce plastic waste; we are committed to creating circular business models and continue to look for innovative ways to accelerate a circular economy. At the same time, we must remind ourselves that the goals of circularity are twofold – to tackle pollution and to reduce the impacts of climate change. Circularity is a key driver in the reduction of greenhouse gas emissions, and so we must consider circularity and net zero emissions as linked when we think about plastic production. At Dow, we see circularity as integral to transforming the waste but also to reaching our 2050 net zero target.
Decarbonizing our manufacturing sites will play a big role in this ambition, and one of our most exciting projects is currently taking place at our ethylene site in Canada where work is underway to remove Scope 1 and Scope 2 emissions from both our existing and new production.
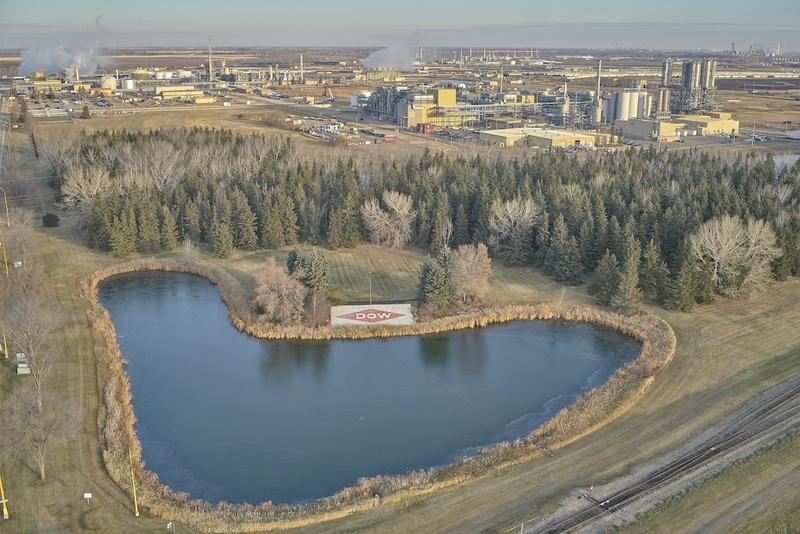
Decarbonization in action: Fort Saskatchewan
Two thousand miles west from the INC-4 negotiations in Ottawa - in Fort Saskatchewan, Alberta - Dow is working to eliminate approximately 1 million MTA (Metric Tons per Annum) of carbon dioxide emissions annually at our plastic production facility. While plastic production has become more efficient in recent years, Dow's investment in the Fort Saskatchewan site aims to make the process more sustainable.
Currently, Dow's plastic manufacturing site in Fort Saskatchewan heats ethylene feedstocks to high temperatures in a cracker to break them down into the molecules we need to make polyethylene plastic. The process requires a significant amount of energy which by consequence creates CO2. This CO2 then traditionally enters the atmosphere.
Recognizing that the bulk of our CO2 emissions come from this process, Dow has been looking at how to reduce emissions and work towards a more sustainable plastic production process. The Path2Zero project at Fort Saskatchewan is Dow's latest step in this right direction, demonstrating how we can implement new technologies and use innovative methods to remove emissions from these crackers.
Working with the Canadian government and industry partners, Fort Saskatchewan will be the world's first net zero scope 1 & 2 emissions integrated ethylene cracker and derivatives site. Dow will retrofit the current crackers at Fort Saskatchewan with the ability to capture the off-gas and convert this into circular hydrogen to be used as a clean fuel for the production process, reducing the need for fossil fuels to power production. In addition, CO2 will be captured onsite and transported and stored by existing third-party CO2 storage infrastructure.
Our two-phase implementation process is set to be completed in 2029, helping to decarbonize 20% of Dow's global ethylene capacity and eliminate all Scope 1 and Scope 2 emissions from the site. This means that the site, despite growing capacity significantly, will reduce 1 million MTA (Metric Tons per Annum) of CO2 emissions. This will not only contribute to Dow's Decarbonize & Grow strategy, which encourages the capture of sustainable growth opportunities while delivering on our 2030 and 2050 emissions reduction targets, but it will also support the Canadian government's 2030 emission reduction milestone to reduce emissions by 40 - 45%.
Two sides of one coin: circularity and decarbonisation
Making our production sites net zero is crucial to achieving our 2050 net zero goal. However, we cannot rely on this in isolation. It is crucial that circularity and decarbonization are considered as two sides of the same coin. Simply decarbonizing our production sites will not be enough to reach net zero emissions. Rather, we need to recognize that circularity for plastics is one of the greatest enablers of reaching net zero emissions in removing emissions from the production process.
It is imperative to understand that the innovation developments in circularity and decarbonization will run in parallel. The crossroads at which they meet will be the ultimate breakthrough aspiration. At Dow we have many dedicated engineers and scientists focused on this space pursuing the ultimate progressive, dynamic objectives of full circularity and decarbonization.
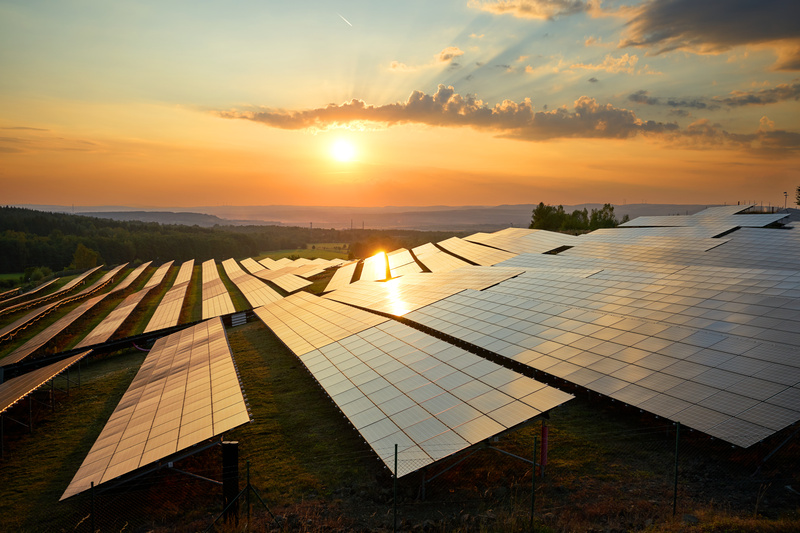
Circularity as a net zero driver; investing in the right partnerships and technologies
When plastic is only used once, we lose a valuable resource. At Dow, we're finding innovative ways to design and retain the plastic's value. Our aim is to build a circular economy where plastic can be used for longer, and then reused and recycled when it reaches its end of life. In this way, we can both reduce the amount of plastic discarded as waste and keep valuable carbon resources in the loop for longer, minimizing the use of fossil resources.
Circularity for plastic starts by designing with recyclability, reduction, and reuse in mind. Designing applications must look to use as few resources and material possible, as well as enabling reuse and recycling without compromising performance or functionality. There's also scope to use innovative packaging design to help shift consumer willingness to recycle and reuse plastic. Then, with the right collection, sorting and recycling infrastructure and technology, plastic waste can be used to create new recycled or circular plastic.
Two complementary recycling technologies - mechanical and advanced recycling - will be vital to reducing emissions in helping to divert waste away from landfills and incineration.
Advanced recycling plays a particularly vital role in decarbonization. As a complementary technology to mechanical, it allows the industry to recycle previously ‘unrecyclable' plastics and turn them back to virgin grade plastic. Research has shown that the most sophisticated advanced recycling processes can save up to 60 per cent of carbon emissions with a cradle-to-grave approach.
At Dow, we are partnering with companies like Mura Technology and Plastogaz, to scale advanced recycling globally, while maintaining our investment in mechanical recycling, so we can realize potential carbon emission and waste savings.
Bio-based feedstocks also need to be part of the equation. Increasing bio-based plastics production from bio wastes and residues reduces carbon emissions from plastic production by minimizing the initial use of raw fossil materials. In May 2023, we announced an exciting collaboration with clean energy creator, New Energy Blue, to develop renewable plastic materials from corn residue. This was a first-of-its-kind agreement in North America which aimed to create bio-based ethylene for Dow's U.S. Gulf Coast assets to produce renewable plastics across fast-growing end-markets.
Canada as the home to pioneering net zero innovation
As with our recycling partnerships, Fort Saskatchewan demonstrates how new and innovative processes can reduce the carbon footprint of the plastics industry. Coupled with circular economy ambitions, we hope that new technologies and collaboration will help us to create a blueprint to reach net zero across our production sites, supporting us on our Decarbonize & Grow progress.
To reach their own emissions and circularity goals, the Canadian government is looking for support from businesses, local administrations, and people.
Pressure isn't just coming from the government; consumers are becoming increasingly conscious of their own impact. And Canada is a country that is willing to embrace change and adapt the plastics industry, spearheading the move towards a net zero future.
Building a net zero plastics industry
Dow's Path2Zero Fort Saskatchewan project is a great example of how governments and the value chain can come together on large scale projects to create positive change for our industry. However, efforts to reduce emissions can't be isolated to infrastructure. We must be even more ambitious. To achieve net zero goals, circularity must be brought into the conversation. Overlooking circularity as a core driver of carbon emissions reduction in the plastic industry is a mistake we cannot afford to make and as technologies improve and develop we must be ever more mindful of connecting the two. As we reflect on INC-4 in Ottawa, we are excited to champion the importance of circularity as part of our vision for a plastic industry fit for the future, and to work collaboratively towards a net zero, waste free future.
Victor Zapata is North America Commercial Vice President at Dow
This article is sponsored by Dow