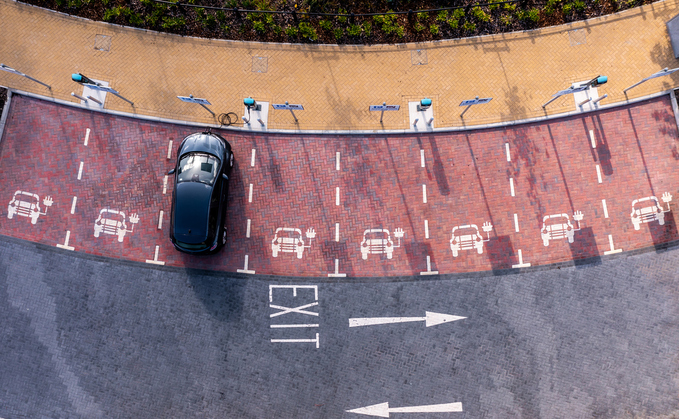
BusinessGreen reports on the fast-evolving plans to establish a thriving EV battery recycling industry in the UK
Batteries are set to become even more ubiquitous than they are already. The clean tech revolution will see battery technologies play a critical role in our cars, our trucks, our power grid, our buildings, and even our ferries. But what happens when these millions of batteries reach their end of life?
Ramping up battery reuse and recycling is increasingly regarded as critical to ensuring climate goals are met in as sustainable and efficient way as possible. Keeping batteries and their constituent metals in circulation for as long as possible not only reduces the economy's dependency on environmentally harmful mining practices, but it provides battery mineral-scarce countries like the UK with a steady, low-carbon stream of metals that reduce its reliance on volatile supply chains.
As one of Europe's largest car markets, there is clearly huge potential for a large battery recycling industry in the UK as more and more vehicles electrify. University of Warwick researchers have calculated more than a fifth of battery metals used for cell production in the UK by 2040 could be supplied by recycling end-of-life batteries, taking a sizable chunk out of import requirements.
But currently, the UK has no industrial capacity for lithium-ion battery reprocessing and recycling, with most lithium-ion EV batteries currently dismantled into modules and then shipped to mainland Europe for material recovery - at considerable expense to the vehicle manufacturer.
It is no surprise, therefore, that there has been a flurry of battery recycling plant announcements in recent months, as investors and companies look to carve out a slice of the nascent market.
A consortium of British car companies, recycler EMR, and academics are working with the government-backed Advanced Propulsion Centre (APC) on RECOVAS, a project which is aiming to result in the UK's "first" commercial-scale recycling facility for EV battery packs. Britishvolt - the company behind plans to build a gigafactory in Northumberland - has inked a deal with mining giant Glencore to develop a lithium-ion battery plant in Kent. And in England's automotive heartlands in the West Midlands electric vehicle (EV) recycling facilities are being plotted by waste management giant Veolia and UK battery recycler Technology Minerals.
These companies are banking on a surge of used EV batteries becoming available to recyclers over the coming years as the first generation of electric cars come offline. Most operators are planning facilities that specialise in both the upcycling of batteries - the testing and repurposing of EV batteries with some life remaining for energy storage - as well as the process of extracting lithium, manganese, cobalt, and nickel from the cells that can then be refined for reuse in new batteries.
But the various projects vying to become the UK's first industrial-scale dedicated EV recycling plant have significant hurdles they need to overcome, from clinching planning permission from an over-stretched and under-resourced Environment Agency, to securing a robust stream of scrap materials to justify their operation, and raising the funds needed to build out capacity.
Some analysts have also pointed to a shortage of scrap batteries in the near-term, given that the first generation of electric vehicle (EV) batteries are still on roads today. Hans Eric Melin, founder of specialist consultancy Circular Energy Storage, told BusinessGreen there was "no chance" for a UK recycler to rely solely on EV batteries alone before 2030, predicting that used EV battery supply would not reach beyond 100,000 tonnes before the end of the decade.
"I think it will take at least 10 years until we have any considerable volumes of electric vehicle batteries," he said. "But what then can be done, and what should be done is, we should have more companies focusing on the on the reuse side of it, because that is really what is happening - that is where you have the value." A large proportion of used cars in the UK get packaged off to third party countries, limiting the number of batteries that will ultimately reach the end of their lives in the UK, he added.
The cost-of-living crisis could further exacerbate the shortage of scrap EV battery materials, he noted, predicting that a slower turnaround of cars as household budgets are squeezed would ultimately feed through to the reycling sector, as would auto companies' current efforts to prioritise selling fewer - but more expensive - cars in response to the global shortage of semiconductors and soaring raw materials costs. Every million EVs not sold means about 16,000 tonnes of cells not being available for reuse or recycling over a 10-year period, he noted on Twitter.
But Robin Brundle, chairman of Technology Minerals, the UK-listed company behind plans to build a lithium-ion recycling plant near Wolverhampton, said there was a strong pipeline of batteries in need of recycling already in the UK.
"The tsunami of the problem is here now," he said. "The number of international companies that have got hundreds of tonnes of lithium-ion batteries already here in the UK which they can do nothing with, tells us the problem is now - it's not 10 years down the road." The Wolverhampton plant will recycle electric bike batteries, toothbrushes, and mobile phone batteries as EV battery supply is ramped up, he said.
"There's a pent-up store [of scrap batteries] that is more than enough to keep our plant going in year one in the UK," Brundle added. "And our plan is to have one new plant here in the UK each year now for the next five years, in order to build up to the bigger capacity that that is that is coming."
Recyclus, a company part-owned by Technology Minerals, claims it will be able to source and recycle 8,400 tonnes of batteries in the first year of operations using its proprietary dry recycling process, a figure that it claims will rise to approximately 41,500 tonnes by 2027. It plans to sell the resulting 'black mass' to companies that can then process it into material that can be used for new batteries and is also hoping to eventually integrate a 'back-end' processing step into its own operations.
Under the plans, which are currently with the Environment Agency for final approval, the plant will not only specialise in recycling battery materials, but in repurposing batteries with some life left in them for energy storage projects.
"We will test them, collect all the energy out of the battery and sent it back to the grid," Brundle explains. "If a battery passes a certain test, then we'll be able to recertify it to go back out for energy storage. But if it doesn't pass that test, we'll process it, shred it, collect the liquid out of it that can be circular, split off the plastic and other bits and pieces, to end up with black mass that has the four critical minerals [lithium, manganese, cobalt and nickel]."
Putative gigafactories will also prove a major source of scrap metal. EV battery manufacturing plants produce a significant number of defective cells and modules, plus thousands of tonnes of 'dry' anode and cathode scrap, all of which require recycling.
Jerry Williams, CEO of battery technology start-up Gigamine, said EV battery manufacturing plants would be a source of battery materials in the near-term. "The key sources now for lithium-ion batteries will be a combination of consumer waste and scrap from battery manufacture," he said. "As we get to beyond 2025 towards 2030, the number of end of life EV batteries coming on the market will start to ramp up."
Gigamine, which was co-founded by prominent green Tory Ben Goldsmith, is aiming to establish its first battery facility at the end of next year, as it works to build out its research and development capabilities across a range of recycling technologies. "It's such a rapidly evolving technology landscape, so placing big bets on a given technology now is risky in its own right, because in two, three, four years' time, you might be dealing with something that's somewhat obsolescent," Williams said.
Williams and Brundle both stressed that environmental permitting processes for recycling plants should be updated to reflect the urgent need to establish a circular battery economy that could reduce the UK's dependence on extractive industries and third-party countries - in particular China - for crucial minerals.
Brundle noted that approvals for the Wolverhampton plant had been frustrated by officials' "analysis paralysis", as well as a "reluctance to engage because its new territory". The plant was designated a high priority project by the EA, but it is yet to get give the greenlight to the plans.
Williams similarly expressed concern that the UK's environmental permitting system was not aligned with the need to ramp up EV battery recycling infrastructure in the UK. "We haven't started to build our first facility, but I think getting the right environmental permissions in place, working with the Environment Agency is, is going to be key," he said. "At the moment, it's not clear that's a particularly fast process. [We would welcome] the ability to have a fast track through that to meet the requirements of the Critical Minerals Strategy."
The government's plans to fast-track planning and environmental permitting processes may have angered green campaigners, but it seems some clean tech firms could stand to benefit from more streamlined planning decisions.
What is clear, however, is that companies vying for a bite of the UK's EV battery recycling and reuse market will need support if they are scale up, especially at a time when economic headwinds and soaring energy costs are presenting a particular challenge to capital intensive manufacturing businesses. The University of Warwick researchers calculated that the break-even point for a battery recycling plant is between 2,500 and 3,000 tonnes annually, provided the chemistry of the batteries processed contain nickel and cobalt.
As such, Brundle said he welcomed the energy price freeze proposed by Prime Minister Liz Truss earlier this month. "As Brits, we're pretty good at trying to weave our way through these challenges - but the pure economics comes into it, doesn't it?" he said. "If you're paying £350,000 a month for your energy, and your bill goes up to one million a month - there are not very many businesses that can withstand that that type of level of increase."
Recyclus' plant is less exposed to these cost increases, he said, because it is not reliant on fossil gas for production and will benefit from selling unspent energy collected from scrap batteries back to the grid. "We're counterbalancing by putting energy in the batteries that we can extract back to the grid, prior to them going in for shredding," he said. "We're not netting off yet. But we do believe that we're not far away in the future from netting off, from an actual site point of view."
Brundle also urged the government to diverge EU regulations and classify black mass as non-hazardous waste, a move that would lift a ban on the import and export of the material and enable a steadier stream of recycled material to UK gigafactories. "Let's make the UK a trading post for black mass, because we need more raw materials to come into the UK," he said. "We simply don't have enough capacity to supply the materials to the gigafactories and the wider 'eco' structure that's supported by the automotive sector. This is critical because if manufacturers can't get batteries, they'll go manufacture and assemble elsewhere."
The economic risks of failing to ramp up the UK's recycling battery chain were also highlighted by Clem Silverman, stakeholder engagement lead at the Advanced Propulsion Centre. He noted that the UK's position as a major automotive exporter could falter if efforts to onshore more of the EV supply chain failed.
"As we transition to net zero and zero emission vehicles, if we don't have that industry embedded in the UK we could lose those opportunities," he said. "It is really important that we embed the EV supply chain here in the UK, so that it's close to where to where our manufacturing is occurring and helps bring down of the embedded carbon in the manufacturing processes. [It can also] ensure we're not reliant on other places for our raw materials and components.
"The closer that is to home the better: better for jobs, better for the levelling up agenda, better for net zero."
The fledgling EV battery recycling industry has a long way to go if it is to become a key component of the net zero transition and a major supplier of crucial green commodities. But it clearly has huge potential to minimise environmental impacts, boost the automotive sector, and curb the UK's reliance on imported metals and minerals. With the lessons of energy dependency on Russia now playing out in real-time, it is a compelling proposition. The question is whether investors, policymakers, and companies have the bandwidth and foresight to make the most out of the opportunities a robust battery recycling system could offer the UK.
This article is part of the Net Zero Commodities Hub, hosted in partnership with Wood Mackenzie.