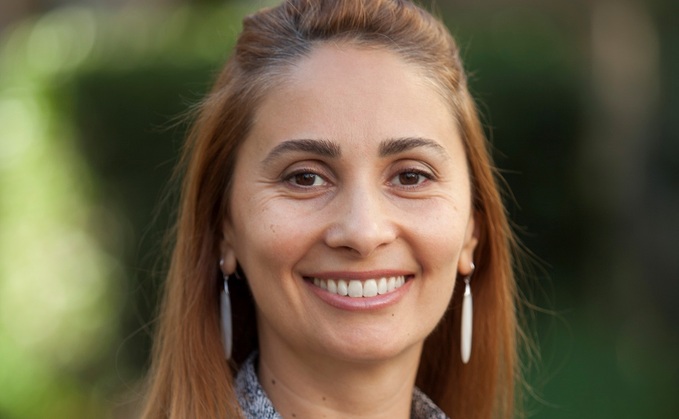
Andreea Moyes is the global head of sustainability at Air bp | Credit: Air bp
Industry Voice: To help meet demand for sustainable aviation fuel (SAF), Air bp underlines the need for a greater understanding of the feedstock landscape, as well as the technology pathways that produce the synthetic kerosene (SK), that is blended with conventional jet fuel to produce SAF
The production of SPK (which is blended up to 50 per cent with conventional jet fuel to produce SAF) starts with one of five main families of raw materials: oils and fats, sugar and cereal, municipal solid waste (MSW), wood and agricultural residue, or renewable energy and carbon.
Image 1:
Each of these feedstocks uses a particular production technology, all of which require approval from the fuel standard body ASTM before being commercially deployed.
In addition, two feedstocks are also approved to produce SAF through co-processing (where the sustainable feedstocks are processed alongside fossil feedstocks through a hydrotreater).
Hydrotreated esters and fatty acids (HEFA)
While HEFA synthetic paraffinic kerosene (SPK) is currently the only commercial pathway being used at scale to produce SAF, current feedstocks (which include waste fats, oils and greases) are limited. Alternative high energy crops that are being trialled or have already been approved as HEFA feedstocks include algae, camelina, pennycress, tallow tree and carinata.
First generation alcohol to jet (AtJ)
The AtJ pathway uses a method whereby sugary, starchy biomass such as sugarcane and corn grain are converted via fermentation into ethanol or other alcohols which can then be shipped or piped before being converted to fuel.
Demand from sectors such as ground fuel and petrochemicals means however that there is limited feedstock available to aviation.
Another consideration with the AtJ pathway is that the reduction in carbon intensity is not as strong when compared to the alternative pathways. The implementation of technologies such as carbon capture and storage technology will be key to lowering greenhouse gas emissions (GHG) using this pathway.
Fischer-Tropsch (FT) for municipal solid waste (MSW)
For SAF produced from MSW using Fischer-Tropsch (FT) technology the main environmental gain is derived from the fact that the waste would otherwise be left to decompose in landfill sites. However, while access to MSW as a feedstock is widely available across the globe, in some regions aviation is in competition with other sectors, including the energy sector, for access to MSW. It is also a capital-intensive process to get the infrastructure in place for this pathway.
There is ongoing work to research and develop technologies that will lead to more efficient SAF production using MSW and reduce the relatively high capital costs. For example, bp and Johnson Matthey co-developed and co-own a simple-to-operate and cost-efficient FT technology that converts synthesis gas, generated from sources including MSW, into long-chain hydrocarbons suitable for the production of SAF.
Technologies to convert second generation biomass
While there are currently no approved pathways for these feedstocks, work is progressing with ASTM for pyrolysis of biomass through both standalone production and co-processing in refineries.
One of the challenges with this pathway is that although agricultural and forestry residue is in vast supply as a feedstock, once aggregated it must be transported by road or rail - as a solid it can't be moved via pipeline. Ultimately this means we'll end up with small production plants near where forestry residues are processed. A handful of these plants do already exist, however none are currently being used to produce SAF.
Fischer-Tropsch (FT) for power-to-liquid (PtL)
Possibly one of the most promising pathways for SAF in the longer term is PtL technology (producing what is known as eSAF). Renewable electricity is used in an electrolysis process to extract hydrogen from water. This green hydrogen is first used to convert carbon dioxide to carbon monoxide. Using FT synthesis technology, this carbon monoxide along with more green hydrogen is then converted into a wax that can be upgraded to SK.
This pathway is still very much in its infancy with eSAF expected in the short-term to be up to around four times the cost of SAF made with HEFA. An increasing focus on using green hydrogen (which is used to produce eSAF) to decarbonise other sectors will benefit aviation and help reduce costs. German mandates already have specific requirements for eSAF from 2026 and European mandates currently being finalised are expected to follow suit in 2030.
The ongoing evolution of PtL and the other production pathways alongside the availability of a wide range of feedstocks is key to scaling SAF production and enabling the decarbonisation of aviation at pace and at scale. As such, Air bp will continue to work with stakeholders and authorities across the energy supply chain to help meet future SAF demand.
Andreea Moyes is the global head of sustainability at Air bp
This article is sponsored by Air bp.