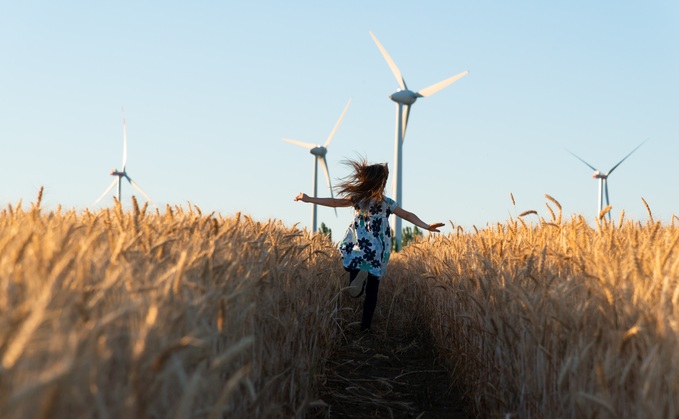
Partner Insight: The recent energy crisis has left a lasting impact with concerns over energy security, cost savings and smart energy management weighing on everyone's minds. Laurie Wood, sector lead for sustainability at BSI, spoke to Sarah Handley, head of sustainability & environmental governance at Siemens Energy, about the company’s successful journey with ISO 50001 Energy Management
Sarah, can you tell us about Siemens Energy?
Siemens Energy is a global leader in the energy sector employing 99,000 employees worldwide operating along nearly the entire energy value chain. In the UK, Siemens Energy employs 6,000 people across more than 15 sites, including manufacturing and service centre locations in Lincoln, Hull, Newcastle, Ulverston, Worcester and Aberdeen.
Siemens Energy portfolio of products and services includes conventional and renewable energy technology, such as gas and steam turbines, hybrid power plants, hydrogen electrolysers, switchgear, and transformers. Siemens Energy includes Siemens Gamesa Renewable Energy (SGRE), a global market leader for renewable energies.
Our mission is to empower our customers to meet the growing demand for energy while transitioning to a more sustainable world. With our innovative technologies and energy experience, we are committed to decarbonising global energy systems and driving the energy transition.
What prompted Siemens Energy to adopt ISO 50001?
There were several key drivers that formed the business case for adopting the ISO 50001:2018 standard for energy management. Firstly, we wanted to achieve compliance with the UK Energy Savings Opportunities Scheme (ESOS) regulation, which implemented the requirements of the EU Energy Efficiency Directive. The ESOS regulations were followed by the ‘Streamlined Energy and Carbon (SECR)' reporting requirements which was also supported by our systematic approach to energy management using the standard. Secondly, Siemens Energy set the target to be Carbon Neutral by 2030 by in our operations which required us to take action to manage our energy consumption/energy mix. We also faced the likelihood of increasing costs if we didn't act, based on the forecast for energy pricing and taxation. And crucially, we believe that Siemens Energy should act as a leader, demonstrating our commitment to decarbonisation by being transparent about energy management in our own operations.
Key Drivers:
- Global targets – Climate Neutral by 2030 in our own operations (Scope 1 & 2)
- Compliance with the Energy Savings Opportunities Scheme (ESOS) regulation implementing requirements of the EU Energy Efficiency Directive
- Expectation of increasing costs due to forecast increases in energy pricing and taxation
- Siemens Energy demonstrating commitment to improvements in energy performance to customers and stakeholders
How does ISO 50001 fit in with any broader goals to achieve net zero?
The ISO 50001 standard focuses on improving energy performance which supports reduction of carbon emission (CO2e) Scopes 1 and 2, to meet our Siemens Energy target to be climate neutral in operations by 2030. Siemens Energy has committed to reducing absolute scope 1 and 2 by 46 per cent by 2025 (based on the 2019 baseline) and 100 per cent green electricity by 2023 (now achieved). Also, in the UK, we have established a Decarbonisation Programme with a dedicated workstream for energy performance for all our site locations that support the overall Siemens Energy Carbon Neutral by 2030 programme and targets.
What were the most accessible and most challenging parts of implementing ISO 50001?
Evidence of the tangible results began promptly after the standard implementation, in part due to making energy a focus for management attention and greater transparency over energy usage and costs.
We also found integrating our existing management systems with ISO 50001 was straightforward due to the similar structure of the standards. Our businesses are certified to ISO 45001 and 14001 and we were able to integrate without adding complexity.
We experienced some early challenges with establishing processes to ensure that energy performance is considered in procurement decisions and for design or products/processes. Typically, procurement decisions are based on cost and quality but introducing energy performance as a criterion has required a change in process.
Communicating the importance of planning and outcomes for energy projects was also challenging. The ISO 50001 standard sets out the process steps required to be able to baseline before improvements are made and to enable verification of the savings/reductions. The rigor required to follow these steps needed to be understood by the local energy teams. The requirement for technical knowledge, for example, energy engineers, was underestimated but we've been able to work through these challenges and get the extra support required.
What were some common blockers you experienced?
- Funding for energy projects
- ROI/payback period seen as too high
- Competence & available resources for delivery of projects, development, and business case, etc
- Length of site lease impacts on investment decisions
- Technology not developed or lack of confidence in solutions
- No additional space on site for energy storage (e.g. for batteries, fuel cells)
What was the biggest lesson learned for Siemens Energy?
The biggest takeaway was the importance of data. Recording data was the most challenging message to convey to energy site representatives, but it is critical to a systematic approach to energy performance improvements. The standard requires recording actual vs expected energy consumption to verify the achievement of objectives and establishment of Energy Performance Indicators.
Were there any quick wins you identified when you first implemented ISO 50001?
Yes, we had several quick wins straight after implementation. For instance, we introduced employee suggestion schemes on our sites which led to some simple changes that made a big difference. Employee awareness is very important as targets changes in behaviour and attitudes to energy use and this can have a big impact. We issued guidelines for temperate settings in offices and manufacturing sites which contributed to energy reduction. We've completed programmes on our sites to install LED lights, curtained airlock doors, destratification fans which have contributed to energy reduction.
What has the impact on your organisation been so far?
Siemens Energy has seen noticeable impacts across our business. We've been able to bring a wider focus on energy and carbon supporting our Climate Neutral and Decarbonisation programmes. We've also seen a heightened awareness of legal compliance across the business and an improvement in the management of internal and external stakeholders. In terms of actual results, we have seen an overall reduction in energy. In the past 3 years we have seen a 50 per cent reduction in gas and a 14 per cent reduction in electricity while increasing turnover. We are continuing to see a reduction in gas and have a target to remove gas for heating on our sites by 2030.
What difference did the standard make during the recent energy crisis?
Maintaining a list of opportunities and potential projects was very helpful; the situation is not static but dynamic, and changing external factors can require a rethink of priorities for funding and execution of energy projects. For example, when energy costs were high the ROI for PV panels was more favourable. Installation of PV panels also makes sense in terms of energy resilience and security with higher energy prices. We now have three sites going for approval of solar PV and battery storage.
Standards and certification are about continual improvement, so what are you planning next?
Currently, not all our sites are certified to the standard. We have brought our Ulverston factory onto the Standard last year (2023). Also, we are merging with Siemens Gamesa Renewable Energy (SGRE) and bringing new sites into our energy management system.
We have made many the quick wins and the obvious changes, but we need to invest in the next steps for replacing gas heating at all our sites. We are looking at options for ASHP and GSHP as options for some site locations. Decisions about further reducing energy costs involve a greater engagement with management on how we use the spaces on site and employee behaviour.
Any tops tips for other organisations looking to implement ISO 50001?
I recommend getting buy-in from senior management at the start of your journey. It's also helpful to link to other legal or customer requirements to show how good management can support stakeholder expectations – e.g. statutory reporting for ESOS, SECR, net zero, and wider stakeholders such as the public and local communities. It's also beneficial to try to focus on building energy teams on-site. One person, often the EHS manager, cannot drive the required actions without support from all other business functions. And, importantly, don't forget that the standard requires technical advice. You should ensure you have expert energy advice available through your facilities management partner or a third party that you can call on.
Why did Siemens Energy choose to partner with BSI?
Gaining formal certification is a rigorous process and careful investment. Our certification partner needed to be a reputable, globally recognized brand with coverage across the requisite standards in all jurisdictions we operate in.
Learn more about ISO 50001 Energy Management and how BSI can help you on your journey by clicking below. As the leading UK certification body, we provide a wealth of resources, tools and expert advice, including training courses and gap analyses, to get you where you need to be.
Laurie Wood is sector lead for sustainability at BSI, and Sarah Handley is head of sustainability & environmental governance at Siemens Energy.
This article is sponsored by BSI.