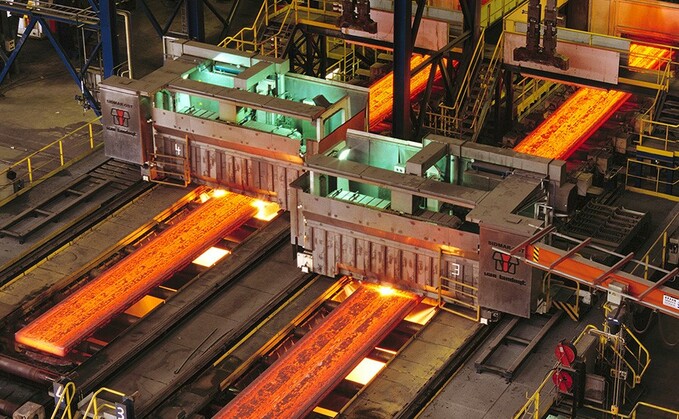
An Arcelor Mittal steel plant | Gredit: Arcelor Mittal
ArcelorMittal, BHP, and Mitsubishi Heavy Industries Engineering broker funding agreement to start work on pioneering carbon capture demonstration units in Belgium and North America
A group of leading global steelmakers, engineering giants, and mining firms have clubbed together to trial carbon capture technology at ArcelorMittal's steel plants in Belgium and North America, with a view to drawing up a design study to enable the system's full-scale deployment..
A funding agreement announced yesterday for the pioneering trial has been brokered between steelmaking giant ArcelorMittal, mining giant BHP, Mitsubishi Heavy Industries Engineering (MHIENG) and Mitsubishi Development Pty Ltd.
The trial involves ArcelorMittal's steel plant in Ghent, Belgium, as well as another unspecified site in North America, and is aimed at identifying means of enhancing the feasibility of carbon capture utilisation and/or storage (CCUS) technologies in the global steelmaking industry.
Used in everything from wind turbines to electric vehicles, steel is a critical material for the net zero transition, but at present production of the metal worldwide remains heavily reliant on fossil fuels, and the industry is estimated to account for seven to nine per cent of global greenhouse gas emissions.
Various technological solutions for the hard-to-abate sector are being developed and rolled out, including using hydrogen and electrification to replace fossil fuels in the steelmaking process, but CCUS is also being touted as a potential means of decarbonising existing CO2-intensive blast furnaces.
According to the International Energy Agency (IEA), CCUS technology may need to be applied to more than 53 per cent of primary steel production by 2050 - equivalent to 700 million tonnes per year of CO2 - in order to deliver a net zero global economy by 2050.
At present, however, there are no full scale operational CCUS systems in place to capture the CO2 from blast furnace steelmaking plants, although ArcelorMittal is planning to commission a demonstration system at its five million tonnes per year capacity factory in Ghent later this year.
Dubbed the Steelanol project, the demonstration plant has been designed to capture carbon-rich process gases from the blast furnace and then covert the CO2 into ethanol.
Under the new agreement, ArcelorMittal plans to trial the technology at both its Ghent factory and at another location in North America, with MHIENG tasked with supplying its proprietary CCUS technology, and BHP and Mitsubishi Development acting as key suppliers of steelmaking raw materials, as well as acting as leading funders of the trial.
The trial is expected to run for "multiple years", the firms said. The first phase in Ghent will involve separating and capturing the CO2 top gas from the blast furnace at a rate of around 300kg a day, while the second phase involves testing the separating and capture of CO2 from the off-gases in the hot strip mill reheating furnace, which burns a mixture of industrial gases, the partners explained.
The firms said they then also plan to install the mobile CCUS testing unit in one of ArcelorMittal's North American direct reduced iron plants. It forms part of the steelmaking giant's global target to reduce its CO2 emissions by 30 per cent by 2030, and by 35 per cent in Europe.
Manfred Van Vlierberghe, CEO for ArcelorMittal Belgium, said decarbonisation of the steel industry was a "huge challenge that we cannot solve alone".
"Alongside our continued energy efficiency improvements, we are developing two routes to decarbonise steelmaking: Smart Carbon and Innovative-DRI," he explained. "Both routes will contribute in our journey to deliver carbon-neutral steelmaking. The Smart Carbon route also allows us to integrate carbon capture and re-use (CCU) or storage (CCS) technologies, capturing carbon emitted during the steelmaking process."
BHP's chief commercial officer, Vandita Pant, stressed that at present there was "no certain or single pathway to net zero for steelmaking", but that CCUS could well play a key role.
"CCUS is one of the key abatement technologies with potential to support development of some of those pathways, so working with industry leaders like ArcelorMittal, Mitsubishi Development and MHIENG, we hope to arrive at scalable solutions more quickly to help reduce carbon emissions in steelmaking," she said. "Steel is a critical product for the world to develop and decarbonise, and we must work hard, together, to enable lower GHG emissions steel, support the reduction of carbon intensity in the blast furnace and test new technologies for steel production."